摘要:隨著第五代移動通信技術(5G 技術)的出現與快速發展,電子產品尤其是智能手機、平板電腦等產品,越發朝著高性能、高集成和微型化的方向發展。功耗成倍的增長將導致電子芯片在狹小空間內產生過高的熱流密度和工作溫度,進一步引發嚴峻的熱失控難題。超薄均熱板具有優異的導熱性能,較大傳熱面積、較好的均溫性能和高可靠性等優點,是解決電子設備散熱問題的首要途徑。為滿足 5G 時代下現代微型化電子設備散熱需求,均熱板進一步超薄化是當前業界和學術界的研究熱點?;诖?,對超薄均熱板傳熱原理進行概述,重點綜述國內外超薄均熱板結構設計研究現狀,包括氣液通道排布結構和吸液芯結構等,介紹目前超薄均熱板封裝制造工藝,并分析其實現極端超薄化中存在的問題,最后對其在高集成超輕薄電子設備等散熱領域的研究趨勢和發展前景進行了科學的展望。
0 前言
2019 年以來,隨著第五代移動通信技術(5G 技術)的出現和快速發展,電子產品尤其是智能手機、平板電腦等產品,越發朝著高性能、高集成和微型化的方向發展。為滿足產品的性能和尺寸需求,電子芯片上的晶體管密度越來越大。
2006 年制造的電子芯片每平方厘米具有晶體管的數量僅可以達到 1 億個,到 2019 年,華為 5G 麒麟 990 芯片已經集成晶體管數量多達 103 億,而該 5G 芯片面積僅為1.13 平方厘米,芯片晶體管的密度增加了接近 100倍。然而,成倍增長的功耗將導致電子芯片在狹小間內產生過高的熱流密度(> 200 W/cm2)和工作溫度(> 70℃),進一步引發嚴峻的散熱問題,導致電子芯片無法正常工作,從而制約其進一步發展。
傳統的電子設備散熱方式,自然對流由于自身換熱系數低,難以滿足更高熱流密度的散熱要求,而強制風冷和水冷熱管理方式需要外加動力裝置,無法適應狹小空間內的封裝集成。新型高導熱材料石墨片具有較高的平面導熱系數(1500 W/m·K),在滿足電子設備散熱方面具有一定的優勢,然而其在厚度方向上導熱系數極差,導熱性能受到限制。因此,開發新型高效的熱管理技術,實現電子產品的有效散熱是當今行業迫切需要解決的問題。
相變傳熱元件利用工質的相變潛熱來帶走熱量,是解決電子設備散熱問題的最具有潛力熱管理方式。為滿足現代微型化電子設備散熱需求,常規尺寸的相變傳熱元件難以應用到產品中,微型化相變傳熱元件,尤其是厚度超薄化的相變傳熱元件,是當前業界關注的焦點。
一般而言,超薄相變傳熱元件包括超薄熱管和超薄均熱板。超薄熱管通常是先制造出管壁超薄的圓熱管,再通過加熱相變壓扁的方式加工而成。目前,大批量生產的圓熱管壁厚最薄可達 0.08 mm,壓扁加工后超薄熱管厚度最低為 0.4 mm,在智能手機三星 Galaxy S7 上得到應用。然而,當厚度進一步降低時,超薄熱管傳熱性能大幅度惡化。更重要的是,采用圓熱管壓扁制備而成的超薄熱管,在薄壁圓管直徑限制下,寬度極為有限,0.4 mm 厚的超薄熱管寬度最多不超過 3 mm,超薄熱管的尺寸無法根據電子芯片尺寸(長寬通常為 10 mm)及實際散熱需求進行變更,超薄熱管散熱能力也因此受到限制。
隨著 5G 時代的到來,超薄熱管逐漸無法滿足便攜式移動電子產品散熱需求。超薄均熱板,通常通過殼板焊接密封成形,外形尺寸可根據實際散熱需求進行調整,同時具有優異的導熱性能,較大傳熱面積和較好的均溫性能等優點,非常適合于 5G 滲透下現代微型化電子設備等領域應用,吸引了廣大研究人員的高度關注。超薄均熱板結合石墨烯輔助散熱是現階段智能手機主流散熱方案。因此,開發出傳熱性能優異超薄均熱板對促進 5G 移動電子設備的發展顯得至關重要。
本文針對超薄均熱板在高集成超輕薄電子器件中的應用,從超薄均熱板的傳熱原理理論,超薄均熱板的結構設計(吸液芯結構與氣液通道排布)以及其封裝制造方法等方面展開敘述,總結了目前超薄均熱板發展現狀,同時對其未來的研究進行了科學的預測和展望。
1 超薄均熱板簡述
超薄均熱板是一種具有超高熱導率的傳熱元件,一般由殼體、支撐柱、真空腔體(蒸汽腔)、吸液芯和工質組成,通過內部工質氣液相變巨大的相變潛熱來實現高效換熱。圖 1 所示為兩種典型的超薄均熱板——沿厚度方向和沿長度方向傳熱的工作原理示意圖。
圖 1 兩種典型超薄均熱板的傳熱工作原理
超薄均熱板完成內部氣液循環相變傳熱的過程包括蒸發端浸潤在吸液芯中的液體工質通過殼體傳遞吸收熱源熱量,在真空腔體內發生蒸發相變變成蒸汽工質,液-氣相變迅速帶走大量熱量,蒸汽工質在真空腔內蒸汽壓差推動下快速流動,迅速擴散至冷凝端;在冷凝端,蒸汽工質通過殼體傳遞被冷源帶走熱量,發生冷凝相變變成液體工質,氣-液相變快速帶走大量熱量,液體工質在吸液芯毛細壓力驅動下發生回流,流動至蒸發端繼續吸收熱量,完成整個氣液循環。
這里兩種典型超薄均熱板傳熱不同之處在于,蒸發端和冷凝端位置,傳熱方向、蒸汽和液體流動方向不同,一種是沿著厚度方向傳熱,可以通過大面積冷凝帶走更多熱量;一種是沿著長度方向傳熱,可以傳遞較遠距離并且保持優異的均溫性能。一般來說,整體厚度小于 2 mm 的均熱板稱為超薄均熱板。隨著 5G 時代的到來,厚度進一步降低的超薄均熱板需求日益突出。實現厚度進一步減小 (<0.4 mm) , 傳熱性能優異(熱導率>5000 W/(m·K))的超薄均熱板結構設計與制造是目前迫切需要的。有學者針對超薄均熱板工作原理進行的理論和數值分析研究,并從理論角度提出了超薄均熱板優化傳熱性能的方向。
SUBEDI 等建立了多熱源和多散熱器下超薄均熱板傳熱理論模型(溫度和壓力分布),分析了絲網吸液芯幾何尺寸包括絲網直徑,分離間隔和厚度等因素對其極限傳熱功率的影響。結果表明,絲網吸液芯的厚度通過影響其毛細極限對超薄均熱板極限傳熱能力具有重大影響;此外,超薄均熱板極限傳輸功率還受限于電子設備正常運行的最高溫度。
LEE 等針對絲網吸液芯超薄均熱板,提出了超薄均熱板極限傳熱能力與絲網吸液芯毛細性能、重力影響、蒸汽擴散阻力與液體流動阻力的理論計算關系,計算了超薄均熱板傳熱熱阻與等效熱導率與吸液芯厚度關系。研究結果說明,超薄均熱板最大傳熱能力隨著吸液芯厚度的增加而增大,然而,等效熱導率卻隨著吸液芯厚度的增加而減小。
PATANKAR 等提出一種超薄均熱板 3D 傳熱數值模型模擬工作過程中熱量傳遞,氣液界面相變和蒸汽流動等,并通過模擬仿真對比分析發現離散溝槽雙孔式冷凝吸液芯結構可以有效改善超薄均熱板冷凝端溫度均勻性,相比于均勻溝槽冷凝吸液芯超薄均熱板,離散溝槽雙孔式冷凝吸液芯超薄均熱板冷凝端溫差降低 37%。此外,該團隊還提出一種基于超薄均熱板的熱阻網絡模型來分析熱阻與工質性能、輸入功率和幾何參數之間的關系,揭示了工質液體品質因數和蒸汽品質因數對超薄均熱板傳熱性能的影響機理,并指出當超薄均熱板厚度減小時,選擇工質應該優先考慮工質的蒸汽品質因數,這也說明隨著超薄均熱板厚度越來越小,蒸汽對其傳熱性能的影響作用越來越大。
CHANG 等結合試驗和數值仿真分析,以氣液相變過程傳熱機理為基礎,提出了超薄均熱板等效熱導率 keff 的半經驗測試方法,如圖 2a 所示。研究結果表明,等效熱導率與超薄均熱板的厚度、傳熱方向和傳熱功率等參數直接相關,并且當超薄均熱板厚度范圍在 0.3~0.5 mm 時,厚度參數對其傳熱性能具有重大影響。
圖 2 超薄均熱板的傳熱理論研究
李聰基于流體相變傳熱傳質理論建立了超薄均熱板穩態運行時熱阻理論模型,研究了不同輸入熱功率和蒸汽腔厚度對超薄均熱板熱阻的影響。結果表明,當蒸汽腔厚度減小至0.3 mm 以后,超薄均熱板熱阻急劇增加,并且隨著蒸汽腔厚度進一步減小,蒸汽流動產生的熱阻占據超薄均熱板總熱阻的比重也越來越大,如圖 2b 所示。這也說明極限超薄厚度均熱板傳熱性能下降主要來源于蒸汽腔。通過以上研究可知,隨著均熱板進一步的超薄化,吸液芯與蒸汽腔厚度均被進一步壓縮,進而導致均熱板傳熱性能急劇下降。在常規超薄厚度下,液體在吸液芯中的流動是設計制造超薄均熱板首要考慮因素;然而,在極端超薄厚度條件下,蒸汽在真空腔體內的流動阻力隨著蒸汽腔厚度減小而急劇增大,逐漸成為另一個阻礙超薄均熱板氣液運行的關鍵因素。
此外,蒸汽腔厚度極小時,由于尺寸效應會導致蒸汽通道內液塞形成,阻礙蒸汽流動,還會抑制液體發生相變過程,進而嚴重影響超薄均熱板的傳熱性能。因此,要實現極端厚度下超薄均熱板的氣液運行,要綜合考慮吸液芯結構與蒸汽腔空間設計。
2 超薄均熱板結構設計
由超薄均熱板的傳熱工作原理可知,氣液蒸發/冷凝相變、蒸汽擴散和液體回流是超薄均熱板正常運行的重要環節。要實現超薄均熱板氣液循環運行,內部要滿足壓降平衡,即吸液芯驅動液體流動的毛細壓力 ?Pcap,要能夠克服蒸發段到冷凝段蒸汽流動阻力 ?Pv,冷凝段到蒸發段液體流動阻力和液體重力壓降 ?Pg,實現液體順利回流至蒸發段。?Pcap≥?Pv+ ?Pl+ ?Pg (1)
保證這些環節的順利進行,主要通過優化氣液通道排布降低蒸汽流動阻力,同時也需要設計吸液芯結構提高吸液芯毛細壓力并降低液體流動阻力。優化設計氣液通道排布和吸液芯結構是實現超薄均熱板的高性能和進一步超薄化的關鍵,也是目前行業界與學術界高度關注的焦點。2.1 氣液通道排布設計
根據超薄均熱板的氣液通道排布方式可分為氣液異面與氣液共面結構排布,兩種排布類型的超薄均熱板氣液運行與傳熱機理示意圖如圖 3 所示。
圖 3 氣液異面與氣液共面結構超薄均熱板傳熱示意圖
由圖 3a 可知,氣液異面超薄均熱板蒸汽通道和液體通道在厚度方向(Z 軸)上是相互分離的,并且蒸汽流動與液體流動在不同的平面(XOY 平面)進行。
圖 3b 所示為新型氣液共面超薄均熱板氣液運行與傳熱機理示意圖,該類型超薄均熱板蒸汽通道和液體通道在厚度方向(Z 軸)上是不可分離的,并且蒸汽流動與液體流動在同一平面(XOY 平面)內進行。兩種氣液運行與傳熱過程類似,都是蒸發段吸液芯中的工質液體吸收外界輸入熱量,發生蒸發相變變成工質蒸汽,并在壓差作用下沿著蒸汽腔長度方向(Y 軸)流動流至冷凝段,工質蒸汽在冷凝段被帶走熱量,發生相變凝結變成工質液體,并在吸液芯毛細壓力推動下流回至蒸發段,進行下一步吸熱蒸發過程。超薄均熱板在穩定運行下,氣液循環持續不斷地進行著。兩種不同的是,氣液異面超薄均熱板氣液相變方向與厚度方向(Z 軸)一致,氣液共面超薄均熱板氣液相變方向則與寬度方向(X 軸)相同。目前的研究中超薄均熱板氣液排布方式只有這兩種結構,以下分別對這兩種氣液排布的超薄均熱板進行了綜述。
2.1.1 氣液異面
沿厚度方向傳熱均熱板通常需要在上下殼板(蒸發端和冷凝端)布置兩層吸液芯,中間支撐出蒸汽腔空間,類似“三明治”結構,是一種典型的氣液異面超薄均熱板結構。
STRUSS 等報道了一種厚度為 0.61 mm 的氣液異面硅基超薄均熱板,采用蝕刻法加工直徑 5 μm,間隔 5 μm 和高度 40 μm 的陣列微針結構作為吸液芯,分布在上下殼板上,采用蝕刻法加工高度較高、周邊帶有微溝槽的支撐柱支撐上下殼板,留出中間蒸汽腔厚度為 0.13 mm,如圖 4 所示。該類超薄均熱板主要應用于沿厚度方向傳熱的大面積熱源與冷源散熱,由于一般需要兩層吸液芯,限制了超薄均熱板厚度進一步降低。
圖 4 “三明治”氣液異面超薄均熱板
針對便攜式移動電子設備狹小空間散熱需求,超薄均熱板沿著長度方向傳熱具有更優的均溫性,能夠有效保證芯片熱量快速傳遞至電子設備殼體,散熱效率高,同時只需要一層吸液芯,厚度相比于“三明治”結構均熱板更低。
SHI 等報道了一種厚度為 0.65 mm 的氣液異面超薄均熱板,采用陣列微柱作為支撐柱,與吸液芯結構在厚度方向上相互分離。YANG 等制造了厚度為 0.53~0.6 mm 氣液異面超薄均熱板,液體通道采用微納結構復合泡沫銅,蒸汽通道則采用電鍍法在銅板上加工出陣列圓柱作為支撐柱,支撐柱之間的空間作為蒸汽腔,支撐柱另一端與吸液芯接觸,實現氣液異面結構設計。
CHEN 等設計制造了一種厚度僅為 0.43 mm 的氣液異面銅超薄均熱板,該超薄均熱板采用口徑為 46 μm(300 目)絲網作為吸液芯,濕法蝕刻加工支撐柱作為蒸汽腔,吸液芯和蒸汽腔在厚度方向上相互分離,兩者厚度分別為 0.15 mm 和 0.08 mm,如圖 5 所示。大量學者均采用該類氣液異面結構(蒸汽腔層為柱狀支撐柱組成的腔體,吸液芯層為整層多孔結構)的設計制造超薄均熱板。
圖 5 支撐柱-吸液芯分離氣液異面超薄均熱板與此同時,“雙絲網”氣液異面結構——粗孔絲網作為蒸汽腔,細孔絲網作為吸液芯的超薄均熱板也被廣泛學者采用。OSHMAN 等采用三層口徑76 μm 銅絲網作為吸液芯,大口徑(0.823 mm)尼龍絲網作為蒸汽腔,制備了厚度為 1.31 mm 的聚合物超薄熱板,如圖 6a 所示。該超薄均熱板粗尼龍絲網與細銅絲網在厚度方向上相互分離,尼龍絲網形成大口徑提供蒸汽流動通道,銅絲網小孔徑具有較好的毛細壓力,為液體流動提供流動通道和驅動力,氣液相變在尼龍絲網與銅絲網接觸界面上發生,是一種典型的氣液異面結構。LEE 等制造了厚度為0.67 mm 的“雙絲網”氣液異面銅超薄均熱板,該超薄均熱板采用 3 層粗孔銅絲網作為蒸汽腔,1 層親水處理過的細孔銅絲網作為吸液芯,如圖 6b 所示。類似的氣液異面結構設計,LIEW 等也分別制造了厚度為 1 mm 和 1.5 mm 的超薄均熱板。
圖 6 “雙絲網”氣液異面超薄均熱板2.1.2 氣液共面
由于內部空間充足,傳統均熱板的吸液芯與蒸汽腔基本都是氣液異面結構設計,氣液運動在不同平面進行,相互之間的干擾較少?,F有的超薄均熱板大部分都是采用氣液異面結構設計,并通過減小吸液芯結構的厚度或者蒸汽腔的厚度來實現均熱板變薄。但是,氣液異面超薄均熱板的總體厚度始終需要計算吸液芯結構與蒸汽腔厚度之和,目前很難實現 0.4 mm 以下厚度的超薄化。而 5G 時代下電子設備越來越緊湊,電子設備內部留給散熱元件的空間被進一步壓縮,這一趨勢促使超薄均熱板往小于0.4 mm 的厚度下探。而超薄均熱板厚度的進一步降低,勢必會減小蒸汽腔厚度,進而導致超薄均熱板蒸汽阻力急劇增大。此外,隨著蒸汽腔厚度的進一步減小,液體工質厚度方向小尺度毛細作用下,在蒸汽腔空間內形成液膜,進一步阻礙蒸汽流動,同時也抑制液體工質相變過程(與沸騰過程中所提及的膜態沸騰類似),稱為液塞,會導致超薄均熱板傳熱性能急劇下降,甚至失效。
華南理工大學湯勇教授團隊創新性地提出氣液共面新型氣液通道排布方式,將蒸汽通道(蒸汽腔)與液體通道(吸液芯)排布在厚度方向上的同一平面上,蒸汽和液體流動在同一平面上進行,超薄均熱板總體厚度可進一步下降。另外,通過氣液通道的交替設置,氣液共面均熱板在寬度方向可以較好地擴展,特別適用于散熱面積較大的場合。這逐漸受到其他研究者的關注。
HUANG 等對氣液異面和氣液共面兩種超薄均熱板的蒸汽與液體流動阻力進行了理論和數值模擬分析,如圖 7 所示,超薄均熱板內部空間厚度越小,氣液通道最優配比下的氣液共面結構超薄均熱板的蒸汽與液體流動阻力總和相比于氣液異面結構超薄均熱板更小。氣液共面結構在總腔體厚度不變的情況下,通過犧牲寬度方向上的空間來保證厚度較大的蒸汽通道,這隨著超薄均熱板整體厚度的減小將表現出越來越大的優勢。
圖 7 兩種排布結構均熱板流動阻力與內部空間理論關系
目前,壓扁型超薄熱管大多采用與氣液共面相類似的結構設計。ZHOU 等將粉末或者絲網吸液芯置于圓管中間,通過相變壓扁法制備得到厚度范圍為 0.4~1.0 mm 的超薄熱管,還研究了吸液芯與蒸汽腔的配比關系對超薄熱管傳熱性能的影響。然而,基于氣液共面結構超薄均熱板的公開報導極其少。Lü 等采用超親水絲網吸液芯制備了尺寸為 100 mm × 50 mm × 0.95 mm 氣液共面超薄均熱板,測試結果表明該均熱板可以傳遞熱流密度 490 W/cm2以上。之后,又采用該結構制備厚度僅為 0.5 mm 的氣液共面超薄均熱板,并采用可視化試驗研究了傳熱過程中蒸汽和液體流動現象,如圖 8 所示。
圖 8 氣液共面超薄均熱板及其氣液排布結構HUANG 等采用四條螺旋編織絲網和底層平織絲網作為吸液芯,制造了厚度為 0.5 mm 的氣液共面超薄均熱板,測試了不同灌注量和擺放位置下超薄均熱板的傳熱性能,如圖 9 所示。研究結果表明,超薄均熱板在灌注量為 100%時具有最優的傳熱性能,此時水平放置下超薄均熱板的傳熱極限功率為 7.58 W;順重力放置可以有效提高超薄均熱板傳熱性能,順重力放置下的超薄均熱板等效熱導率高達 25200 W/(m·K)以上。
HUANG 等還進一步優化了吸液芯排布結構,將螺旋編織絲網增加至六條以提高毛細性能,保持超薄均熱板厚度為 0.5 mm,有效提高了超薄均熱板極限傳熱功率至 10 W。LIU 等對比了不同螺旋編織絲網下超薄均熱板的傳熱性能,研究結果表明,尺寸為 110 mm× 15 mm ×0.41 mm 的超薄均熱板,排布三條編織絲網具有最優傳熱性能,在順重力放置下能夠傳遞最大傳熱量 6 W。
圖 9 編織絲網間隔分布氣液共面超薄均熱板
最近,華南理工大學湯勇教授團隊開發出厚度僅為 0.25 mm±0.03 mm 的氣液共面結構超薄均熱板,采用親水處理的螺旋編織帶作為吸液芯,測試結果表明該超薄均熱板等效熱導率可達 10000 W/(m·K)以上。這說明氣液共面結構是實現超薄均熱板進一步超薄化,突破目前超薄均熱板臨界厚度(0.4 mm)的關鍵。
2.2 吸液芯結構設計
超薄均熱板的吸液芯結構具有驅動液體工質回流、提供液體工質流動通道、促進工質氣液相變和將殼體熱量傳遞至液體工質等功能,是均熱板完成內部氣液循環的重要部件之一。根據超薄均熱板吸液芯結構的不同類型,可以將其分為微溝槽型、粉末燒結型、泡沫金屬型、絲網燒結型和復合結構型。此外,隨著微納加工技術的興起,微納復合尺度吸液芯也受到高度關注。
2.2.1 微溝槽吸液芯
微溝槽吸液芯具有結構簡單、滲透率高的優勢,通常用于加工硅基、鋁基均熱板。LIM 等采用激光加工制備了深度為 0.3 mm 的扇形微溝槽吸液芯,并封裝制造成尺寸為 56 mm × 8 mm × 1.5 mm 的超薄銅均熱板,如圖 10 所示。該超薄均熱板測試輸入功率到 13 W 時才出現燒干現象,并且在功率 8 W 時熱阻為 5.45 ℃/W。
圖 10 激光加工微溝槽吸液芯超薄均熱板CHEN 等設計了一種厚度為 2 mm 的縱橫交錯微溝槽吸液芯鋁超薄均熱板,采用沖壓工藝成型加工殼板,微銑削技術加工出表面覆蓋顆粒結構的微溝槽作為吸液芯,并采用丙酮作為工質,如圖 11 所示。測試結果表明,該鋁基超薄均熱板在水平測試下最大傳輸功率可達 160 W 以上,在 140 W 時達到最小熱阻,熱阻值為 0.156 ℃/W。
圖 11 微銑削微溝槽吸液芯超薄均熱板
PAIVA 等提出了尺寸為 100 mm × 30 mm × 2 mm 的鋁基超薄均熱板,采用平行金屬線陣列結構作為微溝槽吸液芯,同時也作為真空腔體的支撐柱,如圖 12 所示。測試結果表明,在不同工質(丙酮、甲醇和水)下該超薄均熱板極限傳熱能力分別為0.19 W,0.23 W 和 1.25 W。
圖 12 平行金屬線微溝槽吸液芯超薄均熱板
DING 等制造了尺寸為 30 mm × 30 mm ×0.6 mm 鈦基超薄均熱板,通過蝕刻加工高深寬比陣列微柱吸液芯,并采用化學氧化法在微柱表面生長了一層頭發狀納米鈦結構。通過傳熱性能測試試驗可知,該超薄均熱板最大等效熱導率為 350 W/(m·K)。
總體來說,微溝槽具有加工簡便,成本低等優點,但是相對于其他吸液芯,微溝槽吸液芯毛細力較小,液體工質回流速度較慢,會導致超薄均熱板均溫性能較差。
2.2.2 粉末燒結吸液芯
粉末燒結吸液芯具有高毛細壓力,是常規厚度均熱板最常用的吸液芯之一。LI 等采用枝狀粉末燒結作為吸液芯,封裝并測試了尺寸為 100 mm × 50 mm × 2 mm 的超薄均熱板,如圖 13 所示。測試結果表明,在水平測試下,該均熱板能夠有效傳遞120 W 熱量,熱阻僅為 0.196 ℃/W,等效熱導率是銅板的 4 倍以上。
圖 13 粉末燒結吸液芯超薄均熱板
ZHANG 等系統地研究了不同粒徑、不同形貌的銅粉燒結吸液芯,該吸液芯加工有交錯互通槽,結果證明該吸液芯能夠有效促進氣泡成核、生長和脫離,提高超薄均熱板界面相變傳熱性能。LI 等采用 900 ℃高溫燒結制備了不同粒徑銅粉燒結吸液芯,并通過可視化試驗測試了該吸液芯毛細性能,優化粒徑參數。
粉末燒結吸液芯雖然具有較大毛細壓力,但是其滲透率較低,尤其是超薄均熱板應用粒徑更小的粉末,進一步降低滲透率。更重要的是,在極限超薄化條件下,粉末燒結吸液芯往往僅有數層粉末結合,結合力較小而容易導致脫落,從而會大幅度降低超薄均熱板傳熱性能甚至完全失效。
2.2.3 泡沫金屬吸液芯
泡沫金屬吸液芯通常具有較高的毛細壓力和較大的孔隙率。YANG 等提出一種微納結構復合泡沫銅作為吸液芯,制造了總厚度為 0.53~0.6 mm 的超薄均熱板,如圖 14 所示。并研究了注液量、微納結構、泡沫銅層數以及蒸汽腔厚度對超薄均熱板性能的影響。結果表明,泡沫銅層厚度越大、蒸汽腔厚度越大,超薄均熱板傳熱性能越好,并且厚度輕微的增加能夠導致超薄均熱板傳熱性能極大的提升。研究中,超薄均熱板等效導熱系數可以達到 2207 W/(m·K),極限傳熱功率可達 22.66 W 以上。
圖 14 泡沫金屬吸液芯超薄均熱板
然而,與粉末燒結吸液芯類似,泡沫金屬結構孔隙較高,并且分布不規則,導致其結合強度不夠牢固,力學性能較低,且制備工藝較為復雜,成本較高,限制其在極限超薄化均熱板吸液芯的應用。
2.2.4 絲網燒結吸液芯
絲網吸液芯是近年來針對均熱板厚度需求開發出來的,具有孔隙率大、厚度更薄、結構規則、柔性較好等優點,非常適用于目前均熱板超薄化需求。XU 等燒結四層絲網作為吸液芯,制備有效尺寸為 35 mm × 35 mm × 0.62 mm 的超薄均熱板,研究了強制風冷下超薄均熱板沿著厚度方向的傳熱性能,如圖 15 所示。研究表明,采用該超薄均熱板的和比采用相同厚度銅板下熱源溫度降低了 20℃,并且沿厚度方向上可傳遞最大熱流密度可達 425 W/cm2,具有非常高的極限傳熱能力。
CHEN 等開發了一種具有高性價比且易于大規模推廣的梯度孔隙銅絲網,通過調控絲網內部孔隙梯度分布,能夠有效提高絲網吸液芯結構毛細傳輸性能,同時加速相變過程中的氣泡生長,促進超薄均熱板蒸發端的相變蒸發過程。
SHI 等開發了一種尺寸為 80 mm × 50 mm ×0.65 mm 的超薄均熱板,采用口徑為 76 μm(200 目)的絲網作為吸液芯,通過蝕刻圓柱支撐柱來支撐蒸汽腔體,蒸汽腔體高度為 0.2 mm。該研究探索了傾斜角度和注液量等參數對超薄均熱板傳熱性能的影響,發現該超薄均熱板在輸入功率為 7.1~13.7 W 時具有較好的傳熱性能,在最優注液量下,超薄均熱板表現出較低的熱阻(1.2 ℃/W)。
圖 15 絲網燒結吸液芯超薄均熱板
HUANG 等采用一層大口徑(0.89~1.58 mm)粗絲網作為蒸汽腔,兩層小口徑(154~77 μm)細絲網燒結作為吸液芯,制備了尺寸為 100 mm × 65 mm ×1.26~1.77 mm 的超薄均熱板,研究了不同口徑絲網、不同冷卻水溫和不同放置角度對超薄均熱板傳熱性能的影響,如圖 16 所示。其中最優超薄均熱板(SP2,厚度 1.58 mm)可以傳遞熱量 50 W 以上,在50 W 下熱阻僅為 0.107 ℃/W,等效熱導率可達5 000 W/(m·K)以上。類似的,LEIW 等采用大口徑尼龍絲網作為蒸汽腔,3 層口徑為 76 μm(200 目)銅絲網通過電沉積工藝結合在一起作為吸液芯,并在絲網表面利用原子層沉積法加工了超親水涂層,最終開發了有效尺寸為59 mm × 50 mm × 1mm的超薄均熱板。測試結果表明,該超薄均熱板最高可傳遞熱量 40 W。
圖 16 絲網燒結吸液芯超薄均熱板
根據絲網燒結吸液芯超薄均熱板研究現狀可知,絲網是超薄均熱板最具有應用前景的吸液芯之一,然而,絲網吸液芯仍存在毛細壓力較低的不足。
2.2.5 復合結構吸液芯
復合結構吸液芯一般是結合上述吸液芯優點,制備出具有更優異性能的超薄均熱板。OSHMAN 等采用溝槽復合絲網結構作為吸液芯,制造了尺寸為 40 mm × 40 mm × 1.2 mm 的聚合物超薄均熱板,如圖 17 所示。該團隊研究了超薄均熱板在不同重力加速度和輸入熱功率下的傳熱性能,結果表明,在 40 W 熱輸入功率下,超薄均熱板在加速度為 0~10g 的等效熱導率為 1653~436 W/(m·K)。
HUANG 等采用銅粉絲網復合燒結作為吸液芯,制備了尺寸為 220 mm × 50 mm× 1.34 mm 的超薄均熱板,并將其成功應用到質子交換燃料電池輔助散熱。結果表明,采用該銅粉絲網復合燒結吸液芯超薄均熱板后,燃料電池工作溫度與其表面最低溫的溫差降低至 0.5℃。
圖 17 絲網復合溝槽吸液芯超薄均熱板
DENG 等提出均勻徑向發散溝槽復合銅粉結構作為均熱板蒸發端吸液芯,并研究了銅粉口徑、形狀以及加熱面積對均熱板傳熱性能的影響。測試結果表明,該均熱板能夠傳遞高達 280 W/cm2的熱流密度,而熱阻僅為 0.15 ℃/W。此后,CHEN 進一步優化溝槽銅粉復合吸液芯,通過燒結銅粉至Ω 型內凹微溝槽,為蒸汽和液體提供分離的高效流動通道,優化均熱板傳熱性能,并成功將其應用到高功率 LED,降低了 LED 模組基體溫度 27%。
復合結構吸液芯可以結合不同類型吸液芯的優勢,具有較優的綜合毛細性能,但是其復雜的制造工藝與極為有限的吸液芯空間限制了復合結構吸液芯在極限超薄化均熱板中的應用和發展。
2.2.6 微納復合尺度吸液芯
近年來快速發展的微納加工技術為超薄均熱板提供了新型復合多尺度吸液芯的選擇。RYU 等采用混合化學溶液NaClO2,NaOH和Na3PO4·12H2O在泡沫銅吸液層和微柱制備一層納米結構,有效提高微柱吸液芯的毛細性能,可傳遞最大熱流密度相比對照組增加超過 150%,并且具有超高等效換熱系數(heff >5 W/(cm2·K))。
JI 等提出采用納米結構來調控超薄均熱板蒸發端和冷凝端潤濕性,進而提高超薄均熱板傳熱性能。對比了三種超薄均熱板 IE-IE(蒸發端與冷凝端均親水),SIE-IC(蒸發端超親水,冷凝端親水)和SIE-SOC(蒸發端超親水,冷凝端超疏水)的傳熱性能,發現樣品 IE-IE,SIE-IC 和 SIE-SOC 在相同測試條件下熱阻依次降低。
WEN等提出一種化學蝕刻法在燒結絲網吸液芯表面生長納米草和微多孔結構,如圖 18 所示。試驗證明,這兩種微納復合尺度結構能夠有效提高在絲網吸液芯毛細性能和極限熱傳輸能力。此外,對比納米草和微孔結構,微孔結構由于具有更低流動阻力和更多汽化成核位點,具有更高的極限傳輸熱流密度。TANG 等采用表面氧化處理法在銅編織絲網表面制備了一層球狀微納結構層,并探索了處理時間與高溫燒結溫度對微納結構層的影響,發現經過 15 min 表面處理與 500 ℃高溫燒結后的編織絲網毛細上升高度比未處理絲網可以提升 60%以上。
圖 18 微納復合尺度絲網吸液芯LUO 等采用單步法電沉積方式加工了森林狀結構作為吸液芯,該結構形成大量的 Ω 型微溝槽,同時其表面具有大量的類似樹枝微納結構,被證明具有優異的毛細性能,如圖 19 所示。測試結果表明,工質無水乙醇在森林狀結構吸液芯中爬升最高高度可以達到 88 mm。采用該樹枝狀吸液芯制造出厚度為 0.6 mm 的超薄均熱板,在 6 W 時溫差僅為1.2℃,等效熱導率可達 12600 W/(m·K)。
圖 19 微納復合尺度吸液芯超薄均熱板
總體來說,在吸液芯表面加工微納復合結構層可以有效提高吸液芯毛細性能,進而提高超薄均熱板傳熱性能,同時微納結構層厚度幾乎可以忽略,非常適用于超薄均熱板厚度極薄下用以強化吸液芯的毛細性能。
綜上所述,目前超薄均熱板厚度難以做到0.4 mm 以下厚度,主要瓶頸在于現有氣液異面結構設計下導致了吸液芯毛細壓力不夠、蒸汽腔厚度太小引起的阻力太大和液塞現象。結合超薄均熱板結構設計研究現狀可知,通過氣液共面結構降低蒸汽腔阻力和阻礙液塞現象的形成,同時采用微納結構復合絲網吸液芯提高吸液芯毛細壓力,是設計制造極限超薄化均熱板的必然趨勢。
3 超薄均熱板殼體材料與封裝方法
超薄均熱板殼體材料與實際應用場景的需求緊密相連。一般來說,絕大部分超薄均熱板殼體材料采用銅,主要是因為銅具有高導熱系數和可加工性,對于實現超薄均熱板優異的傳熱性能具有較大優勢。而其他特殊應用場合,例如對輕量化需求較高的場景如航空航天領域,通常采用鋁殼體超薄均熱板;半導體芯片一體式集成散熱系統,對熱膨脹系數匹配要求極高的場景,則采用硅作為超薄均熱板殼體材料;近年來柔性電子器件快速發展,對超薄均熱板提出新的柔性化需求,聚合物也逐漸成為超薄均熱板殼體材料的焦點。
焊接封裝制造是超薄均熱板主要成形工藝,與殼體材料息息相關,對超薄均熱板正常運行和工作壽命具有重要影響。目前,超薄均熱板常見的焊接封裝工藝主要包括擴散焊、釬焊、熱熔膠熱壓黏接等。
擴散焊一般是在高溫高壓下超薄均熱板上下殼板緊密接觸,兩殼板原子間發生擴散,從而達到密封作用,也稱為固相擴散。該工藝對設備要求高,成本較高,但具有焊接質量好、焊接強度大、無需額外增添焊料等優勢,通常用于銅、鋁等金屬均熱板焊接,是目前超薄均熱板常見的焊接方式。
ISAACS 等采用擴散焊接將多層絲網和殼板焊接起來,封裝成厚度為 0.85 mm 的超薄均熱板,LI 等采用擴散焊接(高溫 850℃ 高壓下保溫 30 min)的方式封裝了銅超薄均熱板。
釬焊則是在焊縫中添加焊料,在利用焊料熔化連接上下殼板,密封超薄均熱板。釬焊雖然需要添加焊料,但是對設備要求不高,只需要燒結溫度達到焊料熔點即可完成焊接,也是目前超薄均熱板常用的焊接方式。焊料焊接對超薄均熱板材料要求較低,僅需要能與材料表面潤濕貼合,可用于金屬銅、鋁、不銹鋼和聚合物高分子超薄均熱板的焊接。例如,YANG 等通過采用高低溫焊料釬焊封裝了 FR4 基超薄均熱板,YANG 等也是通過釬焊方式封裝了厚度為 0.53~0.60 mm 的超薄銅均熱板,焊接溫度為 300℃。
熱熔膠熱壓黏接工藝主要是通過熱塑性聚合物膜來黏接超薄均熱板殼板,具有操作簡便、成本低廉的優點,通常用于高分子聚合物超薄均熱板的密封封裝。例如,LEWIS 等采用氟化丙烯熱壓黏接封裝了聚合物高分子超薄均熱板,熱壓工藝僅需要在 300℃ 和約 500 kPa 的壓力下完成。OSHMAN 等也采用熱壓接合工藝密封聚合物超薄均熱板邊沿,與抽口相接的聚合物邊沿則采用高真空環氧樹脂密封。
綜上所述,目前金屬殼體的超薄均熱板封裝相對比較成熟,但是隨著均熱板進一步超薄化,封裝過程中極薄殼體容易出現坍陷、破裂等問題,可通過優化支撐結構、提高殼板材料硬度和降低封裝溫度等方面進一步完善高可靠性的封裝工藝。而對于柔性聚合物超薄均熱板,采用熱壓黏接技術雖然能夠進行簡便、低成本的封裝,但是仍處于初步探索階段,遠未形成完整、可靠的封裝工藝。提高聚合物超薄均熱板封裝成形的可靠性是實現其大規模應用所面臨的關鍵技術問題。
4 結論與展望
隨著第五代移動通信技術(5G 技術)的出現與快速發展,電子產品尤其是智能手機、平板電腦等產品,越發朝著高性能、高集成和微型化的方向發展。高性能和高集成化的電子芯片在狹小空間內將產生極大的熱流密度和超高的工作溫度,進一步引發嚴峻的散熱問題,導致電子芯片無法正常工作,從而制約其進一步發展。
超薄均熱板具有優異的導熱性能,較大傳熱面積、較好的均溫性能和高可靠性等優點,是解決電子設備散熱問題的首要途徑。為滿足 5G 時代下現代微型化電子設備散熱需求,均熱板極限超薄化是當前業界和學術界的研究熱點。
然而,由于超薄均熱板的研究時間較短,極端厚度下系統的理論研究極度缺乏。并且隨著均熱板厚度尺寸的進一步減小,超薄均熱板蒸汽流動阻力急劇增大,實現氣液循環運行難度大幅度增加。同時過小的尺寸需求也導致超薄均熱板殼體支撐柱、吸液芯與焊接封裝等加工難度增加。
因此,建立極端超薄化均熱板全新系統的理論體系,優化設計吸液芯結構與氣液通道排布結構,開發高效可靠的超薄均熱板封裝制造工藝,對促進超薄均熱板在便攜式輕薄電子設備散熱方面的發展和應用具有重要意義。
此外,針對不同應用場景的需求,如熱膨脹系數匹配和柔性彎曲等,超薄均熱板可通過調整殼體材料,例如采用硅/陶瓷和聚合物基體等,在實現高效傳熱同時實現特殊應用需求。結合目前超薄均熱板研究現狀,研制傳熱性能優異、極端超薄化均熱板,需從以下方面進行考慮。
(1) 加強極端超薄下均熱板的理論研究。
目前關于超薄均熱板的理論大部分為常規尺寸下的氣液流動規律和相變傳熱分析。例如,支撐柱的主要理論設計依據以降低蒸汽流動阻力為主,蒸汽通道尺寸對蒸汽流動阻力的影響規律等。然而,在極端超薄尺寸下,超薄均熱板殼板厚度急劇降低,殼板極易發生塌陷,進而導致超薄均熱板蒸汽通道變形,增大蒸汽阻力。殼板塌陷成為極薄殼板支撐柱設計的首要選擇,而目前殼體形變理論研究較少。
此外,在極端超薄下,蒸汽腔體由于尺寸效應具有一定的毛細力,會吸附液體工質形成液塞,導致蒸汽通道堵塞。液塞現象對于超薄均熱板氣液運行與相變傳熱的理論還有待進一步研究。因此,需進一步針對極端超薄下均熱板殼體支撐結構形變(例如優化支撐結構和提高殼板硬度等)與規避液塞現象(例如增加橫向均布超親水結構來防止液塞形成)等系統的理論研究。
(2) 優化設計氣液共面結構。
目前超薄均熱板主流的氣液通道排布結構主要為氣液異面結構。隨著厚度進一步減小,蒸汽流動阻力急劇增大,進而導致氣液循環難以進行。目前業界量產的氣液異面結構超薄均熱板最薄厚度始終在 0.4 mm 左右,接近基于該結構超薄均熱板的厚度極限,難以進一步突破變薄。在極端超薄化下氣液共面結構對于蒸汽與液體流動具有更小的阻力,是超薄均熱板實現進一步超薄化的較優結構。因此,研制基于氣液共面結構的超薄均熱板,優化氣液通道配比與內部空間排布,是實現超薄均熱板進一步超薄化的關鍵。
(3) 設計高性能吸液芯結構。
目前超薄均熱板吸液芯結構主要為微溝槽、粉末燒結、泡沫金屬、絲網燒結等單一結構與兩種類型的復合結構。然而,單一類型的吸液芯結構通常難以全面調控其孔隙率,毛細壓力、滲透率和整體尺寸,這些因素綜合決定了超薄均熱板吸液芯的優異毛細性能。吸液芯的毛細性能好壞對超薄均熱板性能起到決定性的作用。因此,開發新型高性能吸液芯結構制造方法,結合常用吸液芯結構與微納結構技術,制造多尺度復合吸液芯結構,可以更好地控制更好地控制其孔隙率,毛細壓力、滲透率和整體尺寸,獲取具有更優異毛細性能的吸液芯。
(4) 發展新的超薄均熱板高可靠性封裝制造工藝。
目前針對金屬殼體超薄均熱板的封裝焊接工藝,包括擴散焊接和釬焊等,在極薄殼體下仍然存在一些的缺陷。擴散焊接對設備需求極高,并且需要接近殼體材料熔點溫度進行,這極大限制了高毛細性能微納復合尺度吸液芯結構在超薄均熱板中的應用;回流焊接溫度相對較低,但是需要額外增添焊料,而焊料需要針對不同殼體進行開發,制造工藝復雜。更重要的是,在封裝焊接過程中,高溫容易導致極薄殼體出現燒穿、褶皺和破裂等現象,嚴重影響超薄均熱板運行可靠性。
而聚合物超薄均熱板主要封裝成形技術——熱壓黏接,面臨著微泄露的風險、并且具有不耐腐蝕,不受高溫等不足,并且在反復彎折的情況下殼體連接部分很容易發生開裂,從而導致內部工質泄漏、殼體膨脹等問題,嚴重影響其相變傳熱性能。因此,開發新型高可靠性封裝成形工藝可以進一步促進超薄均熱板的應用和發展。
來源:機械工程學報
-
移動通信
+關注
關注
10文章
2555瀏覽量
69431 -
電子芯片
+關注
關注
3文章
52瀏覽量
14934 -
5G
+關注
關注
1342文章
47876瀏覽量
556106
發布評論請先 登錄
相關推薦
柔性導熱墊有什么作用?怎么使用?
國家專利高端材料-超薄高導熱絕緣氮化硼膜
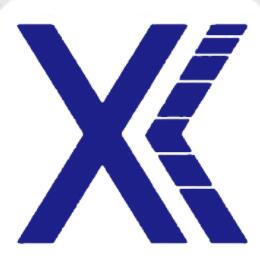
超薄高導熱絕緣の膜材フィルム材料
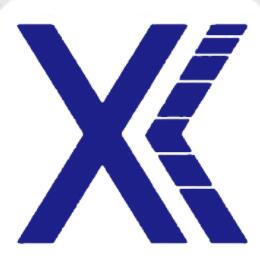
5G高導熱絕緣透波氮化硼膜材の折彎測試
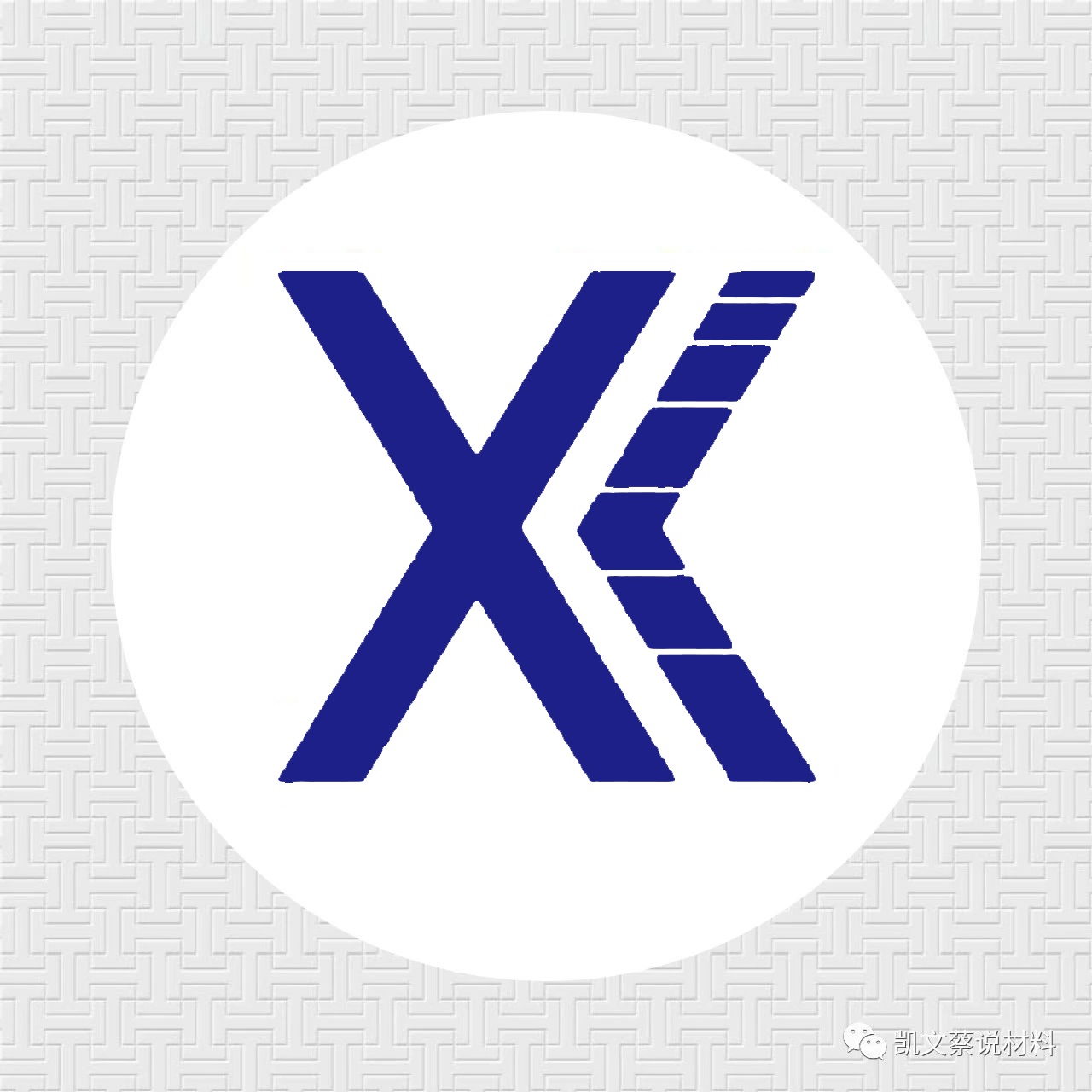
超薄高導熱絕緣氮化硼膜的模切加工
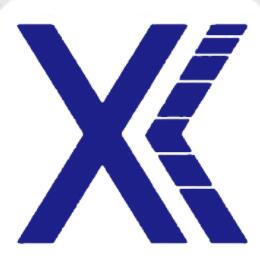
六方氮化硼納米片導熱復合材料的研究進展
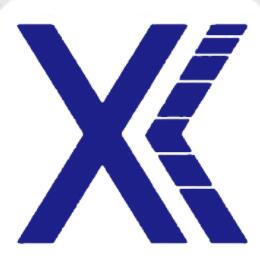
5G新材料超薄高導熱絕緣低介電氮化硼膜材
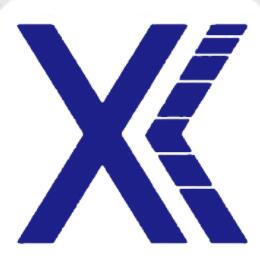
5G高導熱絕緣氮化硼膜材墊片介紹
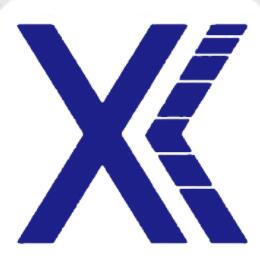
高導熱絕緣氮化硼膜材在5G的應用探討
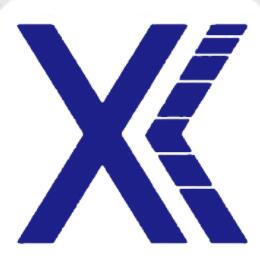
超薄高導熱絕緣氮化硼膜的TG值及耐溫性測試
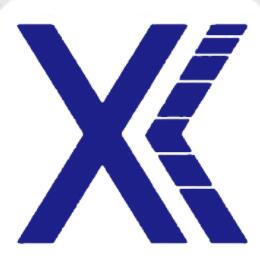
六方氮化硼納米片導熱復合材料及高品質氮化硼粉的介紹
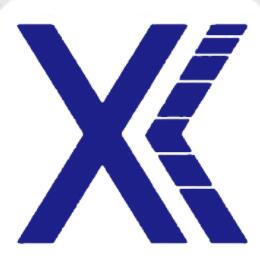
二維氮化硼絕緣高導熱低介電材料介紹應用
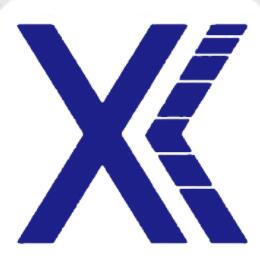
評論